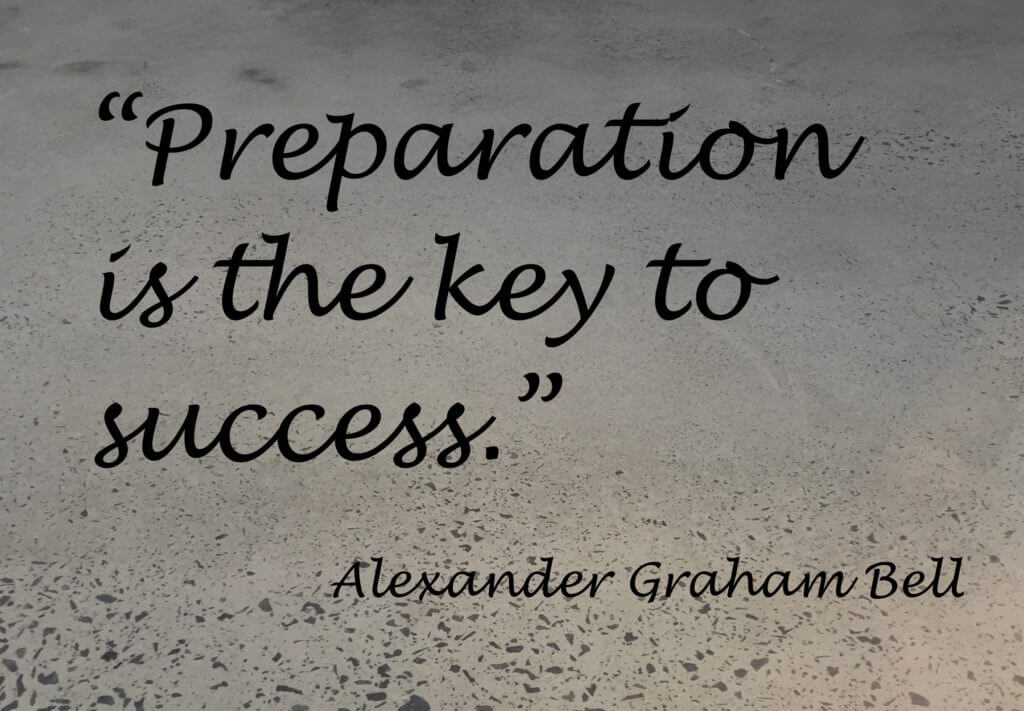
05 Oct Preparing Your Polished Concrete Floor
When Alexander Graham Bell said ‘Preparation is the key to success’ he probably didn’t have concrete flooring in mind but his words are certainly relevant to polishing concrete. Too often The Polished Concrete Company turn up on a project only to find a concrete slab that is very different to what our clients were after. However with a little forethought and preparation you can end up with exactly the polished concrete floor you want.
CALL BEFORE YOU POUR
Before you start your project talk to an experienced concrete polishing company about the look you are trying to achieve. Different finishes have different requirements at the concrete pour stage and while many builders and concreters are familiar with these requirements, some are not. Seemingly insignificant actions on behalf of your concreter can have a huge impact on the end result.
For example, some concreters add retarding agents to the concrete, which affects the polishing process and can react with some concrete sealants. Communication is key. The Polished Concrete Company are always happy to speak to you, your builder or concreter before your project commences.
PLAN YOUR CONCRETE
All concrete is not created equal. There can be large variations between batches of structural concrete such as the amount and type of aggregate used, the colour of the concrete or the concrete’s compressive strength (MPa). Concrete suppliers are obliged to supply structurally sound concrete that will function as a suitable base for construction but aesthetics is not generally a priority. We have seen slabs where the concrete was more brown than grey in colour, which came as a nasty surprise to the clients. Often our clients have seen an image of the type of concrete floor they want without realising that the concrete in the photo is not standard structural concrete at all but custom concrete.
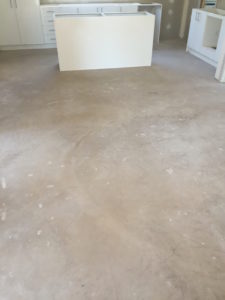
Colour variations between concrete batches are common. This concrete slab was far more brown than grey, much to our clients’ surprise.
If you have your heart set on a particular look, you need to make this clear to your concrete supplier from the outset. They will be able to inform you about the full range of available options – from coloured oxides, to personalised aggregate mixes or hand seeding. The possibilities are endless, but if you don’t ask, you won’t get.
USE AN EXPERIENCED CONCRETE PLACING COMPANY
Aggregate exposure is in the hands of the concreter, not the concrete polisher. Nil, random and fully exposed aggregate all require different actions on behalf of your concrete placer at the time of your concrete pour. The amount of helicopter floating undertaken will also heavily impact the look of your slab. Ensure you deal with professionals who know what is involved in preparing a slab for polishing. The better the slab, the better the finish your concrete polisher can achieve.
PROTECT YOUR CONCRETE DURING CONSTRUCTION
- Ensure contractors are aware that the finished floor will be polished concrete. Use signage if necessary. When heavy objects are dropped or dragged across recently poured concrete they can damage the slab, leading to patches.
- Cover the floor using breathable materials such as linen drop-sheets or Ramboard.
- Do not tape any floor covering directly to the slab, tape can mark concrete.
- Wipe up spills immediately – acidic or oily substances in particular can penetrate deep into a concrete slab, becoming virtually impossible to remove at a later stage.
AVOID PATCHES
A wise concrete polisher once told The Polished Concrete Company, ‘A patch is a patch’. Most scratches, chips and holes can be partially remedied but concrete polishers aren’t miracle workers. While all good concrete polishers have their bag of tricks to ensure patches are colour matched, well blended and flush with the rest of the floor, patches are usually still visible if you were to look for them. Some people love the industrial look. But some people don’t. If you after a flawless finish, protect your concrete and avoid patches.
SCHEDULING MATTERS
Fully exposed polished concrete is a two-stage process. The first stage occurs approximately 10 days after the concrete is poured and sufficiently cured and involves open cut grinding 5 – 8 millimetres of concrete to expose the aggregate beneath. Attempting to grind the floor once walls, cabinetry, pipework etc are already in place can be problematic, so this step needs to take place before construction begins to ensure that the level of aggregate exposure is consistent and the slab is perfectly flat. Most commercial grinding machines can only grind to within 30 millimetres of walls and will not fit into hard-to-reach areas such as cupboards. Edges and areas with restricted access must be ‘hand finished’ using a hand held grinder. Random or nil exposure polished concrete involves only one stage, which generally occurs toward the end of construction. The optimum time to complete nil, random and stage two of full exposure polishing is before cabinetry, doors and skirting boards are in place.